Sorry, but your login has failed. Please recheck your login information and resubmit. If your subscription has expired, renew here.
January-February 2023
It feels like a normal holiday season. ”That was the report I got from the VP of global distribution at one of the country’s best known retail brands on the Monday before Black Friday. He added that the last time he felt that way was November of 2019. One of the perks of this job is that I get to talk to a lot of supply chain executives. In my conversations over the last year, I’ve learned two things. Operations, which was perhaps hardest hit at the start of the pandemic, has learned to operate in this new environment. Sure, there are still hiccups caused by absenteeism and inventory shortages. But those are situational—give them supply and… Browse this issue archive.Need Help? Contact customer service 847-559-7581 More options
Keynote
Supply Chain: The rise of human-centric digital automation
The world of work as we know it has changed dramatically over the last two years to three years. Ongoing labor constraints, a persistent truck driver shortage that’s expected to reach 160,000 by 2030, and continued e-commerce growth have all forced shippers to think harder about how they’ll enable the workforce of the future.
For some companies, the workforce of the future may be more remote in nature and connected via technology. Other organizations will use automation to augment their physical workforces, and still others are coming up with hybrid arrangements that effectively balance available labor with customer demand.
Knowing the importance of these decisions and future states, Logistics Management and Supply Chain Management Review focused this year’s Virtual Summit on Enabling the Workforce of the Future.
Across five distinct sessions and one keynote, the magazines’ editors put today’s game-changing strategies and automated solutions into perspective and offer practical tips for evaluating, implementing and leveraging these tools. These expert presentations will
ensure that your company builds out a workforce that will take your logistics and supply chain operations to the next level now—and well into the future.
On an annual basis, Gartner, Inc.’s analysts research the supply chains of hundreds of companies, taking note of the key trends that those organizations are focusing on and where the companies are investing time and effort.
In response to ongoing labor challenges, Gartner says that today’s leading supply chain organizations are balancing long-term automation investments with other near-term technologies. In most cases, the latter are focused on reducing employee “cognitive overload” and helping organizations prioritize time and focus attention to areas where human performance outdoes that of machines.
In his keynote, Mike Griswold, research VP in Gartner’s Consumer Value Chain team, discusses the challenges that supply chain professionals face when trying to find, hire and retain talent in the current labor market. “It certainly has not gotten any easier over the last several years,” says Griswold, who also focuses on the increasing number of supply chain disruptions and the interconnected nature of those interruptions.
“The frequency and magnitude of disruption is increasing on a global scale,” Griswold says. “It’s really important that this context of disruption serves as a catalyst for us to think about how we want to manage and motivate our associates.”
Griswold also covers the distinct reinventions for supply chain leaders, the focus on human-centric work design and the top supply chain “macro trends.” He explains the value of implementing a future of work strategy, balancing business outcomes with talent outcomes and moving toward the workplace of the future.
“The way we used to work just won’t work anymore,” says Griswold, who ended the session with several specific opportunities and strategies that companies can use to reinvent their own workforces.
Here’s how companies can use automation, technology and other advanced tools to support and nurture their evolving workforces in today’s competitive business environment.
Session 1: Transportation
31st Annual Logistics and Transportation Trends Study: Meeting the need for talent
In this session, Christopher Boone, assistant professor at Mississippi State University, and Karl Manrodt, professor at Georgia College and State University, present the findings of their 31stAnnual Logistics and Transportation Trends study.
Drawing on responses from the more than 300 logistics and supply chain professionals that participated in it, the study reveals impacts that the turbulent market has had on shippers, carriers and service providers. It also focuses on one of the most critical issues and threats facing today’s logistics and supply chain leaders: people.
“We’re seeing more employee-centric factors that are becoming increasingly important to people, and just how they approach work,” says Boone, “and I think we’re seeing that in the results of the survey.”
Boone impresses upon attendees the importance of understanding just how turbulent the environment has been over the last few years. He also mentions that both shippers and carriers have “worked really hard” to adapt and move between different types of transportation in order to meet customer demand.
Boone and Manrodt also discuss the role that technology is playing in helping companies tackle current challenges while also planning for the future. “If you thought transportation was changing rapidly, technology is changing maybe even faster,” Manrodt says, “and the capabilities that are out there are really interesting.”
Session 2: Software
Supply Chain Management Software: The hub of the modern operation
Essential to the efficiency and productivity of modern supply chains, supply chain management (SCM) software helps companies coordinate cut-off times and service levels and better understand how to scale automated systems in order to accommodate peaks in demand.
In this session, Howard Turner, director, supply chain execution systems at St. Onge Company, gives attendees an in-depth look at how companies of all sizes can use SCM to drive efficiency and flexibility.
“This software provides a coordinated view of multiple systems and a centralized way to look at and take action on all of the related information,” says Turner. “Using SCM, companies can make better decisions and get to the point where they truly have visibility into their operations.”
Turned then walks attendees through a case study on China’s acceleration of warehouse automation and discusses the role that software plays in controlling warehouse automation. He also talks about the important role that managers and employees play in the adoption of warehouse software and automation solutions.
“No matter how great a solution it is,” says Turner, “if you don’t have your team on board and you don’t really address the change management, you’re setting yourself up for failure.”
Session 3: Warehouse/DC
2022 WDC Operations Survey: Recalibrating operations and spend
Every year, St. Onge Company partners with Peerless Research Group (PRP) to produce our Warehouse & DC Operations Survey that provides an up-to-date snapshot of current trends in warehouse/DC management. In this session, Don Derewecki, senior consultant, and Norm Saenz, partner and managing director, discuss the many findings of this year’s report.
“This year has been interesting in many aspects,” says Derewecki. “The continuing shortage of available labor to staff operations is a high-level concern going right up into the C-suite.” He goes on to say that the rate of inflation and the interest rate increases have also created complexities for companies. Even so, he says that St. Onge is seeing “high levels of interest in various types of automation and mechanization and information systems upgrades going forward.”
“This was a busy year for warehouse shippers dealing with the tightening labor market, supply chain uncertainties and a growing concern now with the future strength of the economy,” Saenz adds. “The survey shows things aren’t getting any easier for operators.”
While St. Onge is seeing more companies interested in automation, many of those organizations are focused on low-cost process improvement and conventional storage equipment and handling equipment. “There’s an increased demand out there for equipment and technology,” Saenz says, “and that has resulted in some higher costs of goods and longer lead times than we’ve seen in many years.”
Session 4: 3PL
3PLs: Time for collaboration in technology and talent
The continued disruption in logistics and supply chain operations has accelerated the technology transformation within the industry. Due to this ongoing reality, new skill sets are necessary across the board as more technology and automation is integrated into third-party logistics (3PL) operations.
“We’ve been through unprecedented times and knowing that we have not faced one disruption in terms of supply chain capabilities, but many,” says Sarah Banks, managing director, global lead freight & logistics at Accenture. “It’s really caused a critical inflection point for leaders in the supply chain domain to think about what we need to take care of.”
In her session, Banks covers technology and talent; talent engagement capabilities shippers should assess in 3PLs; technologies to attract and retain talent; and talent strategies for shippers and 3PLs. She explains that supply chains are “competitive advantage areas” that 3PLs can use to support revenue and growth.
Banks then walks through the initiatives that companies are prioritizing in the next 12 months and discusses how future-proof supply chains must incorporate a thoughtful and deliberate talent management approach. “And that’s not just on the 3PLs; we also need the shippers to be engaged in that strategy with their logistics partners,” says Banks, “to ensure that the right environment is provided for future workers.”
Session 5: Robotics
Robotics: The “heterogeneous fleet” takes shape
According to a recent Gartner, survey, 86% of companies plan to increase their robotics fleet over time. These companies are exploring various different robotics platforms and figuring out how to both integrate work across a fleet of robots and also integrate those robots with other systems.
The push to implement robotics is largely being driven by the core challenges that fulfillment operations are facing. “If you look at the logistics world today, we’re at a point where we’re looking at the need for transformational change,” says Dwight Klappich, research VP at Gartner.
“Logistics operations are under significant pressure right now and managing different types of orders and distribution models,” he continues. “They have to support omni-channel or hyper-local fulfillment, all during a period of high inflation, high interest rates and increasing cost pressures.”
Companies are also managing ongoing labor constraints and looking to robotics and automation for help, according to Klappich, who discusses the broad spectrum of robotics with a focus on intralogistics smart robots. This is a class of robots that operates primarily within the four walls of the warehouse or DCZ. Intralogistics smart robots can be mobile or stationary, and can operate autonomously or collaboratively
SC
MR
Sorry, but your login has failed. Please recheck your login information and resubmit. If your subscription has expired, renew here.
January-February 2023
It feels like a normal holiday season. ”That was the report I got from the VP of global distribution at one of the country’s best known retail brands on the Monday before Black Friday. He added that the last time… Browse this issue archive. Access your online digital edition. Download a PDF file of the January-February 2023 issue.Keynote
Supply Chain: The rise of human-centric digital automation
The world of work as we know it has changed dramatically over the last two years to three years. Ongoing labor constraints, a persistent truck driver shortage that’s expected to reach 160,000 by 2030, and continued e-commerce growth have all forced shippers to think harder about how they’ll enable the workforce of the future.
For some companies, the workforce of the future may be more remote in nature and connected via technology. Other organizations will use automation to augment their physical workforces, and still others are coming up with hybrid arrangements that effectively balance available labor with customer demand.
Knowing the importance of these decisions and future states, Logistics Management and Supply Chain Management Review focused this year’s Virtual Summit on Enabling the Workforce of the Future.
Across five distinct sessions and one keynote, the magazines’ editors put today’s game-changing strategies and automated solutions into perspective and offer practical tips for evaluating, implementing and leveraging these tools. These expert presentations will
ensure that your company builds out a workforce that will take your logistics and supply chain operations to the next level now—and well into the future.
On an annual basis, Gartner, Inc.’s analysts research the supply chains of hundreds of companies, taking note of the key trends that those organizations are focusing on and where the companies are investing time and effort.
In response to ongoing labor challenges, Gartner says that today’s leading supply chain organizations are balancing long-term automation investments with other near-term technologies. In most cases, the latter are focused on reducing employee “cognitive overload” and helping organizations prioritize time and focus attention to areas where human performance outdoes that of machines.
In his keynote, Mike Griswold, research VP in Gartner’s Consumer Value Chain team, discusses the challenges that supply chain professionals face when trying to find, hire and retain talent in the current labor market. “It certainly has not gotten any easier over the last several years,” says Griswold, who also focuses on the increasing number of supply chain disruptions and the interconnected nature of those interruptions.
“The frequency and magnitude of disruption is increasing on a global scale,” Griswold says. “It’s really important that this context of disruption serves as a catalyst for us to think about how we want to manage and motivate our associates.”
Griswold also covers the distinct reinventions for supply chain leaders, the focus on human-centric work design and the top supply chain “macro trends.” He explains the value of implementing a future of work strategy, balancing business outcomes with talent outcomes and moving toward the workplace of the future.
“The way we used to work just won’t work anymore,” says Griswold, who ended the session with several specific opportunities and strategies that companies can use to reinvent their own workforces.
Here’s how companies can use automation, technology and other advanced tools to support and nurture their evolving workforces in today’s competitive business environment.
Session 1: Transportation
31st Annual Logistics and Transportation Trends Study: Meeting the need for talent
In this session, Christopher Boone, assistant professor at Mississippi State University, and Karl Manrodt, professor at Georgia College and State University, present the findings of their 31stAnnual Logistics and Transportation Trends study.
Drawing on responses from the more than 300 logistics and supply chain professionals that participated in it, the study reveals impacts that the turbulent market has had on shippers, carriers and service providers. It also focuses on one of the most critical issues and threats facing today’s logistics and supply chain leaders: people.
“We’re seeing more employee-centric factors that are becoming increasingly important to people, and just how they approach work,” says Boone, “and I think we’re seeing that in the results of the survey.”
Boone impresses upon attendees the importance of understanding just how turbulent the environment has been over the last few years. He also mentions that both shippers and carriers have “worked really hard” to adapt and move between different types of transportation in order to meet customer demand.
Boone and Manrodt also discuss the role that technology is playing in helping companies tackle current challenges while also planning for the future. “If you thought transportation was changing rapidly, technology is changing maybe even faster,” Manrodt says, “and the capabilities that are out there are really interesting.”
Session 2: Software
Supply Chain Management Software: The hub of the modern operation
Essential to the efficiency and productivity of modern supply chains, supply chain management (SCM) software helps companies coordinate cut-off times and service levels and better understand how to scale automated systems in order to accommodate peaks in demand.
In this session, Howard Turner, director, supply chain execution systems at St. Onge Company, gives attendees an in-depth look at how companies of all sizes can use SCM to drive efficiency and flexibility.
“This software provides a coordinated view of multiple systems and a centralized way to look at and take action on all of the related information,” says Turner. “Using SCM, companies can make better decisions and get to the point where they truly have visibility into their operations.”
Turned then walks attendees through a case study on China’s acceleration of warehouse automation and discusses the role that software plays in controlling warehouse automation. He also talks about the important role that managers and employees play in the adoption of warehouse software and automation solutions.
“No matter how great a solution it is,” says Turner, “if you don’t have your team on board and you don’t really address the change management, you’re setting yourself up for failure.”
Session 3: Warehouse/DC
2022 WDC Operations Survey: Recalibrating operations and spend
Every year, St. Onge Company partners with Peerless Research Group (PRP) to produce our Warehouse & DC Operations Survey that provides an up-to-date snapshot of current trends in warehouse/DC management. In this session, Don Derewecki, senior consultant, and Norm Saenz, partner and managing director, discuss the many findings of this year’s report.
“This year has been interesting in many aspects,” says Derewecki. “The continuing shortage of available labor to staff operations is a high-level concern going right up into the C-suite.” He goes on to say that the rate of inflation and the interest rate increases have also created complexities for companies. Even so, he says that St. Onge is seeing “high levels of interest in various types of automation and mechanization and information systems upgrades going forward.”
“This was a busy year for warehouse shippers dealing with the tightening labor market, supply chain uncertainties and a growing concern now with the future strength of the economy,” Saenz adds. “The survey shows things aren’t getting any easier for operators.”
While St. Onge is seeing more companies interested in automation, many of those organizations are focused on low-cost process improvement and conventional storage equipment and handling equipment. “There’s an increased demand out there for equipment and technology,” Saenz says, “and that has resulted in some higher costs of goods and longer lead times than we’ve seen in many years.”
Session 4: 3PL
3PLs: Time for collaboration in technology and talent
The continued disruption in logistics and supply chain operations has accelerated the technology transformation within the industry. Due to this ongoing reality, new skill sets are necessary across the board as more technology and automation is integrated into third-party logistics (3PL) operations.
“We’ve been through unprecedented times and knowing that we have not faced one disruption in terms of supply chain capabilities, but many,” says Sarah Banks, managing director, global lead freight & logistics at Accenture. “It’s really caused a critical inflection point for leaders in the supply chain domain to think about what we need to take care of.”
In her session, Banks covers technology and talent; talent engagement capabilities shippers should assess in 3PLs; technologies to attract and retain talent; and talent strategies for shippers and 3PLs. She explains that supply chains are “competitive advantage areas” that 3PLs can use to support revenue and growth.
Banks then walks through the initiatives that companies are prioritizing in the next 12 months and discusses how future-proof supply chains must incorporate a thoughtful and deliberate talent management approach. “And that’s not just on the 3PLs; we also need the shippers to be engaged in that strategy with their logistics partners,” says Banks, “to ensure that the right environment is provided for future workers.”
Session 5: Robotics
Robotics: The “heterogeneous fleet” takes shape
According to a recent Gartner, survey, 86% of companies plan to increase their robotics fleet over time. These companies are exploring various different robotics platforms and figuring out how to both integrate work across a fleet of robots and also integrate those robots with other systems.
The push to implement robotics is largely being driven by the core challenges that fulfillment operations are facing. “If you look at the logistics world today, we’re at a point where we’re looking at the need for transformational change,” says Dwight Klappich, research VP at Gartner.
“Logistics operations are under significant pressure right now and managing different types of orders and distribution models,” he continues. “They have to support omni-channel or hyper-local fulfillment, all during a period of high inflation, high interest rates and increasing cost pressures.”
Companies are also managing ongoing labor constraints and looking to robotics and automation for help, according to Klappich, who discusses the broad spectrum of robotics with a focus on intralogistics smart robots. This is a class of robots that operates primarily within the four walls of the warehouse or DCZ. Intralogistics smart robots can be mobile or stationary, and can operate autonomously or collaboratively
SC
MR


Latest Supply Chain News
- Despite American political environment, global geopolitical risks may be easing
- Joseph Esteves named CEO of SGS Maine Pointe
- Employees, employers hold divergent views on upskilling the workforce
- April manufacturing output slides after growing in March
- Q1 sees a solid finish with positive U.S.-bound import growth, notes S&P Global Market Intelligence
- More News
Latest Podcast

Explore
Business Management News
- Joseph Esteves named CEO of SGS Maine Pointe
- Employees, employers hold divergent views on upskilling the workforce
- April manufacturing output slides after growing in March
- Q1 sees a solid finish with positive U.S.-bound import growth, notes S&P Global Market Intelligence
- 6 Questions With … Sandeep Bhide
- MIT CTL offering humanitarian logistics course
- More Business Management
Latest Business Management Resources

Subscribe

Supply Chain Management Review delivers the best industry content.
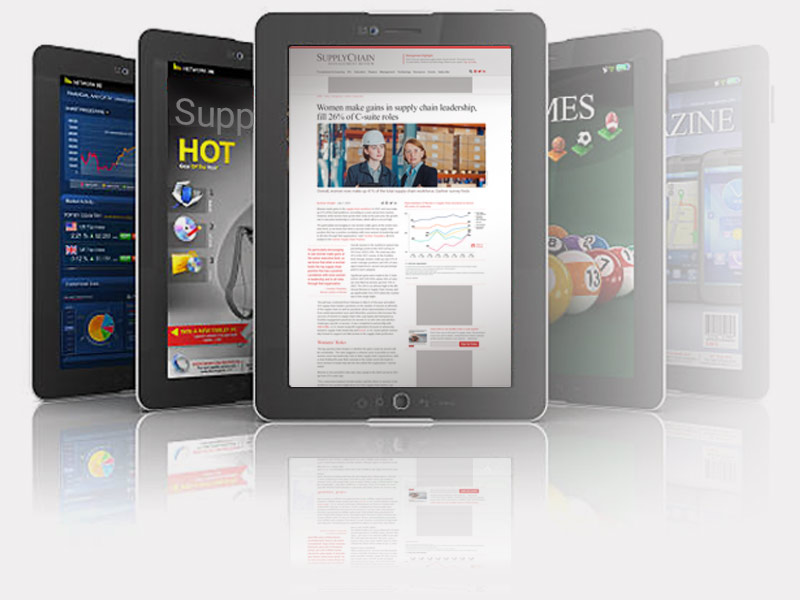
Editors’ Picks



