Sorry, but your login has failed. Please recheck your login information and resubmit. If your subscription has expired, renew here.
July-August 2023
Most business people have heard the phrase “move fast and break things.” But how do you move fast, break things, and remain profitable? Inside this issue of Supply Chain Management Review are the answers—we hope. We have two articles this month that address decision-making. The articles (“Chain reaction: Isn’t it nice when your supply chain just works?” and “Managing like ‘Maverick’ in today’s turbulent, dynamic environment”) approach the topic of decision-making from decidedly different perspectives, but I believe they are more similar than they appear. Browse this issue archive.Need Help? Contact customer service 847-559-7581 More options
As supply chains continue to evolve to meet the needs of a post-pandemic world, processes and systems have to be transformed accordingly. Organizations are, therefore, investing more time and resources to undertake change management projects within and across supply chain functions. As part of these efforts, each organization must establish how it will decide if the change has been successful and evaluate the success of these initiatives.
Major type of change: Digital transformation
Supply chain organizations have undergone numerous types of transformations in recent years, with one of the most prominent being digital transformation. Data from APQC’s research shows that organizations are heavily invested in this type of change. As shown in Figure 1, more than 70% of organizations surveyed by APQC are in the midst of a digital transformation. This includes conducting pilot projects, evaluating a pilot project, or undergoing full-scale adoption.
Check out the related infographic from APQC: How to measure change management success
Put another way, nearly half of organizations (49%) have moved beyond their pilot projects to either evaluating initial results or implementing a full-scale digital transformation. Nearly one-fifth of organizations (16%) have progressed to the point at which they have initiated continuous improvement efforts.
Figure1: Current state of adoption of digital transformation in supply chain
Source: APQC
Figure 2 shows the wide variety of components in organizations’ digital transformations. Most of the items are important to supply chain operations and performance. However, the component that the largest percentage of organizations is implementing or upgrading is their ERP system, which has a large impact on supply chains. The rest of the components vary in complexity, from moving systems to the cloud to engaging in robotic process automation.
For these changes and others that affect the supply chain, organizations must establish a robust plan for measuring the success of the change. Organizations should first agree upfront on what success looks like and what indicators will be used.
Figure 2: Top 10 components of digital transformation
Source: APQC
Measuring change initiatives
Organizations must identify the measures that they will use to assess success that support their business and supply chain goals. They should agree upfront on a well-balanced set of measures that yield actionable insights into performance. Selected measures should help identify current challenges and opportunities, as well as align with the organization’s culture and strategic goals.
What this means in practice varies depending on organizational needs. Many organizations take a phased approach that focuses on adoption measures earlier in the rollout, then shifts to success or impact measures toward the end of implementation. This can account for the human factors in a change rollout that are not always easy to quantify.
Figure 3: Frequency of change management measures used
Source: APQC
APQC research finds that organizations tend to use a mix of technical (e.g., project milestones) and value measures (e.g., satisfaction and benefits realization) to track their change initiatives. Fewer than one-third of organizations use behavioral measures (e.g., adoption, compliance, or behavioral change) to monitor if the change itself sticks or becomes engrained in employee behavior. It’s important to use all three types of measurements to get a holistic picture of the effectiveness of the change (Figure 3).
The top two measures used by organizations are key project milestones and employee feedback. Overall, organizations should seek to use a mix of technical measures focused on the project as well as value measures that gauge satisfaction. It’s important to also track behavioral measures such as compliance or observations of behavioral change. Fewer organizations use these types of measures, perhaps due to the variability of how this information is collected and interpreted.
Be aware of the influence of selected measures
Selecting the right measures for any initiative can be a struggle for organizations, and picking measures for change management in supply chain is no different. Ensuring that measures align with organizational priorities is only one part of the effort. Tailoring measures to business and supply chain goals as well as the phases of the change will provide the most helpful data on the change’s progress.
Leaders should recognize, however, that the measures adopted will drive employee behavior, sometimes in unintended ways. Setting measures communicates throughout the organization that certain actions and targets are most important, thus guiding employees toward behaviors that ideally both further the change and achieve goals.
Moreover, the types of measures an organization selects can influence how effective a change initiative is perceived to be. In APQC’s research, organizations that used the following measures achieved higher rates of perceived effectiveness for their change than those that didn’t:
- key communication milestones;
- speed of change execution;
- adoption or utilization measures; and
- stakeholder satisfaction.
APQC respondents reported that other measures did not prove to significantly affect the perceived effectiveness of a given change.
Organizations need to identify how they are going to collect data in ways that ensure accurate information that spans the change process. Identifying the sources of employee engagement data is only one part of measuring the success of change.
Gathering relevant data
APQC finds that change management is ultimately about people, their fears or anxieties about change, and the best ways to alleviate those fears or anxieties so they are willing to participate in change. While organizations may agree on some quantitative measures of change, there will always be a dimension of change that is more qualitative in nature. Some organizations may find it difficult to collect quantitative data early in the journey. This is where qualitative data, such as success stories or illustrations of positive sentiment, can help drive buy-in among skeptics by providing evidence that the change is having a positive and productive impact.
Prior to starting a change initiative in supply chain, organizations can use change assessments such as readiness surveys to gather information. The assessment can gauge whether employees are ready for the change and how it will affect their jobs. The organization can then use this information to guide how it rolls out any transitions to ensure greater employee buy-in and minimize resistance. The organization can also take the assessment results and develop a timeline that considers employee sentiment as well as any other changes that can affect the rollout of the transition.
During the transition, the organization may want to conduct additional change assessments to understand the degree to which employees are adopting or resisting the changes. This can inform the organization of any adjustments needed to the change management efforts as the rollout
continues. For example, if employees do not understand the vision and objectives of a change, leadership can provide additional communication on the reasoning behind the transition.
Employee surveys are not the only method of collecting data on change management. As shown in Figure 4, although surveys are used by a majority of organizations, supervisor observations and employee feedback systems also provide insight.
The largest groups of organizations rely on a combination of data provided by surveys and more subjective information collected through supervisor observations and employee feedback. To a lesser extent, some organizations hold focus groups to have employees provide input on the transition, and some conduct social listening to quantify employee sentiment.
The methods used by the largest groups of organizations involve more straightforward data collection. Although social listening may provide valuable information on how employees perceive change when not filtered through interaction with supervisors, it requires more resources to both collect employee sentiment and analyze it in a way that provides unbiased input.
Figure 4: Methods used to track employee engagement in change
Source: APQC
Taking action
Selecting the right measures to track change is an ongoing challenge for many supply chain organizations. But APQC research finds that leading organizations have found effective ways to measure and track change both quantitatively and qualitatively:
- agree upfront on measures of success;
- make a phased approach that draws in different measures at different stages of change;
- remain aware of how measures drive behaviors;
- leverage qualitative observations to track the emergence of new values and behaviors; and
- remain flexible.
These strategies and approaches help organizations assess the progress of change, drive buy-in, and pinpoint areas of resistance or change fatigue more effectively.
Building flexibility into change plans can also positively affect the perception of change. This enables an organization to evaluate if a change initiative is on the right path, whether in execution or measurement. If adjustments need to be made along the way, the organization is able to make changes to ensure that the change initiative meets business and supply chain targets and is sustainable.
About APQC
APQC helps organizations work smarter, faster, and with greater confidence. It is the world’s foremost authority in benchmarking, best practices, process and performance improvement, and knowledge management. APQC’s unique structure as a member-based nonprofit makes it a differentiator in the marketplace. APQC partners with more than 500 member organizations worldwide in all industries. With more than 40 years of experience, APQC remains the world’s leader in transforming organizations. Visit us at apqc.org and learn how you can make best
practices your practices.
SC
MR
Sorry, but your login has failed. Please recheck your login information and resubmit. If your subscription has expired, renew here.
July-August 2023
Most business people have heard the phrase “move fast and break things.” But how do you move fast, break things, and remain profitable? Inside this issue of Supply Chain Management Review are the answers—we… Browse this issue archive. Access your online digital edition. Download a PDF file of the July-August 2023 issue.As supply chains continue to evolve to meet the needs of a post-pandemic world, processes and systems have to be transformed accordingly. Organizations are, therefore, investing more time and resources to undertake change management projects within and across supply chain functions. As part of these efforts, each organization must establish how it will decide if the change has been successful and evaluate the success of these initiatives.
Major type of change: Digital transformation
Supply chain organizations have undergone numerous types of transformations in recent years, with one of the most prominent being digital transformation. Data from APQC’s research shows that organizations are heavily invested in this type of change. As shown in Figure 1, more than 70% of organizations surveyed by APQC are in the midst of a digital transformation. This includes conducting pilot projects, evaluating a pilot project, or undergoing full-scale adoption.
Check out the related infographic from APQC: How to measure change management success
Put another way, nearly half of organizations (49%) have moved beyond their pilot projects to either evaluating initial results or implementing a full-scale digital transformation. Nearly one-fifth of organizations (16%) have progressed to the point at which they have initiated continuous improvement efforts.
Figure1: Current state of adoption of digital transformation in supply chain
Source: APQC
Figure 2 shows the wide variety of components in organizations’ digital transformations. Most of the items are important to supply chain operations and performance. However, the component that the largest percentage of organizations is implementing or upgrading is their ERP system, which has a large impact on supply chains. The rest of the components vary in complexity, from moving systems to the cloud to engaging in robotic process automation.
For these changes and others that affect the supply chain, organizations must establish a robust plan for measuring the success of the change. Organizations should first agree upfront on what success looks like and what indicators will be used.
Figure 2: Top 10 components of digital transformation
Source: APQC
Measuring change initiatives
Organizations must identify the measures that they will use to assess success that support their business and supply chain goals. They should agree upfront on a well-balanced set of measures that yield actionable insights into performance. Selected measures should help identify current challenges and opportunities, as well as align with the organization’s culture and strategic goals.
What this means in practice varies depending on organizational needs. Many organizations take a phased approach that focuses on adoption measures earlier in the rollout, then shifts to success or impact measures toward the end of implementation. This can account for the human factors in a change rollout that are not always easy to quantify.
Figure 3: Frequency of change management measures used
Source: APQC
APQC research finds that organizations tend to use a mix of technical (e.g., project milestones) and value measures (e.g., satisfaction and benefits realization) to track their change initiatives. Fewer than one-third of organizations use behavioral measures (e.g., adoption, compliance, or behavioral change) to monitor if the change itself sticks or becomes engrained in employee behavior. It’s important to use all three types of measurements to get a holistic picture of the effectiveness of the change (Figure 3).
The top two measures used by organizations are key project milestones and employee feedback. Overall, organizations should seek to use a mix of technical measures focused on the project as well as value measures that gauge satisfaction. It’s important to also track behavioral measures such as compliance or observations of behavioral change. Fewer organizations use these types of measures, perhaps due to the variability of how this information is collected and interpreted.
Be aware of the influence of selected measures
Selecting the right measures for any initiative can be a struggle for organizations, and picking measures for change management in supply chain is no different. Ensuring that measures align with organizational priorities is only one part of the effort. Tailoring measures to business and supply chain goals as well as the phases of the change will provide the most helpful data on the change’s progress.
Leaders should recognize, however, that the measures adopted will drive employee behavior, sometimes in unintended ways. Setting measures communicates throughout the organization that certain actions and targets are most important, thus guiding employees toward behaviors that ideally both further the change and achieve goals.
Moreover, the types of measures an organization selects can influence how effective a change initiative is perceived to be. In APQC’s research, organizations that used the following measures achieved higher rates of perceived effectiveness for their change than those that didn’t:
- key communication milestones;
- speed of change execution;
- adoption or utilization measures; and
- stakeholder satisfaction.
APQC respondents reported that other measures did not prove to significantly affect the perceived effectiveness of a given change.
Organizations need to identify how they are going to collect data in ways that ensure accurate information that spans the change process. Identifying the sources of employee engagement data is only one part of measuring the success of change.
Gathering relevant data
APQC finds that change management is ultimately about people, their fears or anxieties about change, and the best ways to alleviate those fears or anxieties so they are willing to participate in change. While organizations may agree on some quantitative measures of change, there will always be a dimension of change that is more qualitative in nature. Some organizations may find it difficult to collect quantitative data early in the journey. This is where qualitative data, such as success stories or illustrations of positive sentiment, can help drive buy-in among skeptics by providing evidence that the change is having a positive and productive impact.
Prior to starting a change initiative in supply chain, organizations can use change assessments such as readiness surveys to gather information. The assessment can gauge whether employees are ready for the change and how it will affect their jobs. The organization can then use this information to guide how it rolls out any transitions to ensure greater employee buy-in and minimize resistance. The organization can also take the assessment results and develop a timeline that considers employee sentiment as well as any other changes that can affect the rollout of the transition.
During the transition, the organization may want to conduct additional change assessments to understand the degree to which employees are adopting or resisting the changes. This can inform the organization of any adjustments needed to the change management efforts as the rollout
continues. For example, if employees do not understand the vision and objectives of a change, leadership can provide additional communication on the reasoning behind the transition.
Employee surveys are not the only method of collecting data on change management. As shown in Figure 4, although surveys are used by a majority of organizations, supervisor observations and employee feedback systems also provide insight.
The largest groups of organizations rely on a combination of data provided by surveys and more subjective information collected through supervisor observations and employee feedback. To a lesser extent, some organizations hold focus groups to have employees provide input on the transition, and some conduct social listening to quantify employee sentiment.
The methods used by the largest groups of organizations involve more straightforward data collection. Although social listening may provide valuable information on how employees perceive change when not filtered through interaction with supervisors, it requires more resources to both collect employee sentiment and analyze it in a way that provides unbiased input.
Figure 4: Methods used to track employee engagement in change
Source: APQC
Taking action
Selecting the right measures to track change is an ongoing challenge for many supply chain organizations. But APQC research finds that leading organizations have found effective ways to measure and track change both quantitatively and qualitatively:
- agree upfront on measures of success;
- make a phased approach that draws in different measures at different stages of change;
- remain aware of how measures drive behaviors;
- leverage qualitative observations to track the emergence of new values and behaviors; and
- remain flexible.
These strategies and approaches help organizations assess the progress of change, drive buy-in, and pinpoint areas of resistance or change fatigue more effectively.
Building flexibility into change plans can also positively affect the perception of change. This enables an organization to evaluate if a change initiative is on the right path, whether in execution or measurement. If adjustments need to be made along the way, the organization is able to make changes to ensure that the change initiative meets business and supply chain targets and is sustainable.
About APQC
APQC helps organizations work smarter, faster, and with greater confidence. It is the world’s foremost authority in benchmarking, best practices, process and performance improvement, and knowledge management. APQC’s unique structure as a member-based nonprofit makes it a differentiator in the marketplace. APQC partners with more than 500 member organizations worldwide in all industries. With more than 40 years of experience, APQC remains the world’s leader in transforming organizations. Visit us at apqc.org and learn how you can make best
practices your practices.
SC
MR


Latest Supply Chain News
- Few executives believe their supply chains can respond quickly to disruptions
- Technology’s role in mending supply chain fragility after recent disruptions
- Tech investments bring revenue increases, survey finds
- Survey reveals strategies for addressing supply chain, logistics labor shortages
- Israel, Ukraine aid package to increase pressure on aerospace and defense supply chains
- More News
Latest Podcast
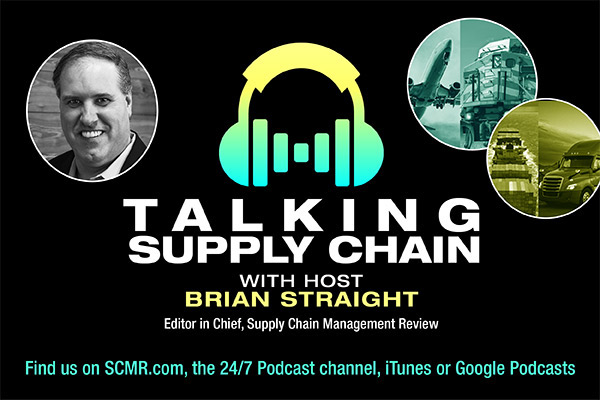
Explore
Procurement & Sourcing News
- Israel, Ukraine aid package to increase pressure on aerospace and defense supply chains
- How CPG brands can deliver on supplier diversity promises
- How S&OP provides the answer to in-demand products
- There is still work to do to achieve supply chain stability
- Blooming success: The vital role of S&OE in nurturing global supply chains
- How one small part held up shipments of thousands of autos
- More Procurement & Sourcing
Latest Procurement & Sourcing Resources
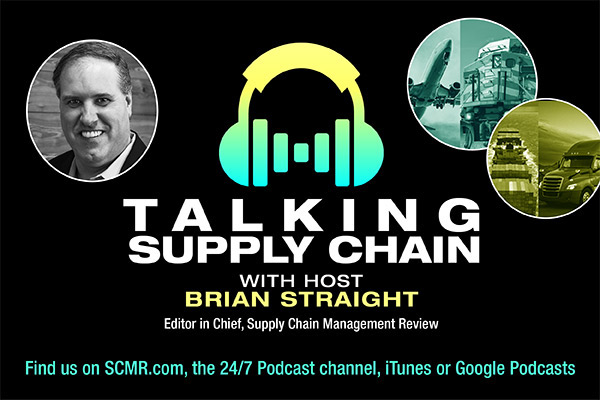
Subscribe

Supply Chain Management Review delivers the best industry content.
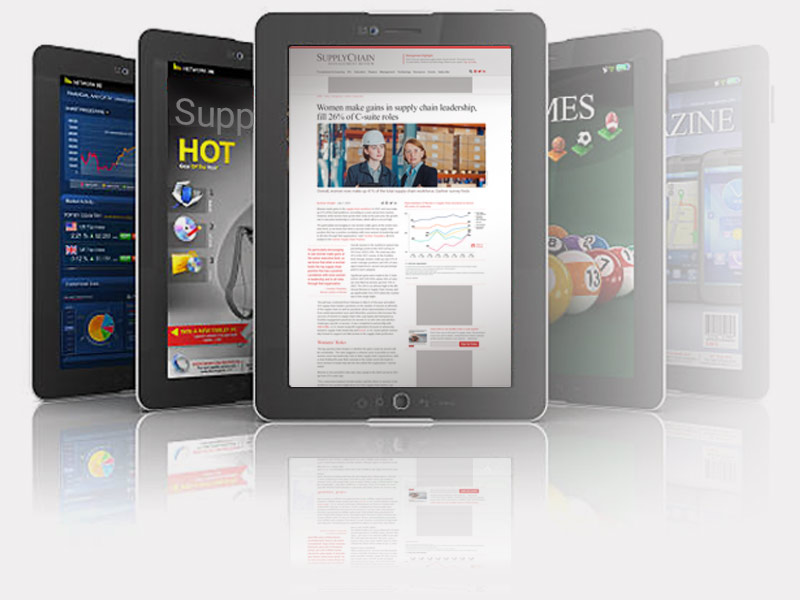
Editors’ Picks



