In this series of posts, I am basically trying to document the process of setting up Sustainable procurement in a company. As sooner or later, this will become a must in each and every organization we work in.
Like anyone, I did not know where to start. If you try to use Google, you will end up in an information overflow, and still without a proper direction.
In my particular case, I have relied on two documents as a base:
ISO20400 Sustainable procurement – Guidance
This is a guide issued by the International Standard for Organization (ISO). It is not a free document, hence I can not share it. As of today (October 2022) there is no possibility to get certified against this standard. However, some consultants audit against the standard, so you can get an independent review of your work.
Ethical and Sustainable procurement by the CIPS.
This publication is only accessible to paid members of the CIPS
Where to start
That is the hard part. Firstly, I had to understand what Sustainable procurement means.
The below diagram is created based on the ISO definition.
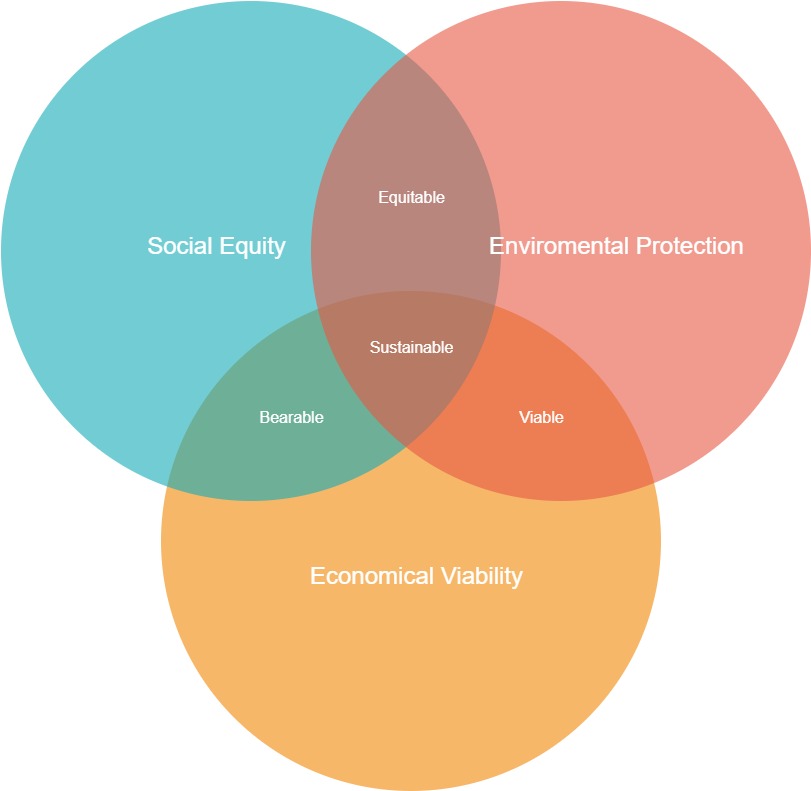
You will as well find quite often companies using ESG – Environmental, social, governance
Environmental | Social | Governance |
● Climate change ● Pollution ● Waste ● Deforestation | ● Human rights ● Modern slavery ● Employee rights ● Child labor | ● Corruption ● Tax ● Executive pay ● Business ethics |
And as well there is the concept of the “Triple bottom line”: People, planet, profit.
As you can see, all this is very similar. Let us not get confused. I have decided to stay with the Social, Environmental, and Economic framework.
Now connecting this to Procurement this would become:
- Social: Labor rights (modern slavery, forced labor, equal pay), Health and Safety, community involvement
- Environmental: climate change (CO2), pollution, packaging, transport, end of life
- Economical: Whole life cost, design, development, fair operating practices
Step 1: Get your policies and procedures in place
Sustainable procurement policy
First, we have to introduce Sustainability in our policies. As we know, policies set up the ground rules, and we want the whole business to recognize the importance of doing business sustainably.
Both papers I use recommend not making a separate policy, but embedding sustainability into the existing policies.
So let us add the below points into the policy, stating that the company’s Supply Chain department will be:
- Fully compliant with the code of conduct and conflict of interest policy.
- Not harming the environment and selecting products that are the best possible solution regarding:
- Reduction of CO2 emission
- Reduction or elimination of pollution
- Using recyclable or reusable materials wherever possible.
- Using sustainable and environment-friendly products wherever possible.
- Working only with vendors who are not violating any human rights or local labor practices, including their Tier 1 suppliers
- Supporting and promoting SMEs and local businesses, as well as community and government initiatives
Standard Operating procedure for implementation of Sustainable practices
Contracts
Adding Sustainability related clauses in the contracts seems like an easy part. Bear in mind, you have to involve legal and finance in the discussion, as this is a significant change in the contract. SEE related clauses should assure:
- Immediate contract termination in cases of the following incidents:
- Slavery or forced labor in the organization or Tier 1 vendors,
- Fraud case in connection to the vendor’s business or connected businesses,
- Corruption or bribery attempts.
- Adding SLA/KPIs related to sustainable practices. This really depends on the nature of the business. They can be using only sustainable consumables, phasing out high energy consumption equipment, etc.
- Assurance of workers’ rights before, during, and after the contract.
- Communication channels and joint audit programs and plans.
Supplier code of conduct
Usually, in procurement, we have a lengthy Terms & Conditions document. This document deals with the commercial and legal part of the business between us and our supplier. The supplier code of conduct focuses on how the supplier is doing his job with respect to its employees.
I have seen quite lengthy documents, going into every possible detail. Let us not forget, you will need to have the capacity to audit the vendors based on this. Hence, try to be as practical as possible. Otherwise, you will end up with an audit non-conformance for your team.
What I would suggest for the Supplier Code of Conduct:
- Employment contracts shall be created and have all clauses as per the local employment law.
- Wages shall be paid out as per the contract, with no deductions outside the ones. allowed by the law (usually for causing damage to the company, mobile phone, etc).
- Defined working hours, overtime pay, and weekly and annual leave.
- No personal documents are to be held by the employer.
- Adherence to health and safety regulations based on the law and specific industry best practices.
- Anonymous employee grievance mechanism.
- Procedures are in place to ensure no harassment or abuse happens at the workplace, in company-arranged accommodations, or in transportation.
- Procedures are in place to ensure no child labor or forced labor is used in the organization.
- Procedures are in place to ensure women’s rights are guaranteed in terms of equal pay, pregnancy, and maternity.
- Audit procedure.
Grievance mechanisms
Usually, in large companies, an anonymous reporting system is already established. But it is more focused on workers’ rights and eventually reporting criminal acts. Here, we are opening the channel up for all stakeholders: suppliers (including their staff), NGOs, clients, and end users. I propose to add a link to the main Company web page, inviting everyone to report cases of any law or business practice violation. However, it shall not stop at the link. A full committee shall be formed, consisting of full-time employees and committee members from the C-suite of the company. Their job is to go through the received notes and action on each. Only then the whole system works, and progress will be made.
Assessment and Audit
The next task would be to create the procedure and forms for Supplier assessment and Supplier audit. Again, it heavily depends on the industry, hence I can not recommend any. I have provided a couple of suggestions on how to do it practically in the following text.
There can be several procedures, focused on environmental protection and labor. Audits need to be exclusively on-site audits, as their goal is not to tick the boxes but to have a realistic picture of the current status.
Step 2: Assess
Identify vulnerabilities and major risks in your Supply Chain
Let us create a risk matrix like the one you are normally doing for assessing your Supply Chain risks. With a twist: now we are dealing with SEE-related risks
For a start, let’s go with a general assessment of the products and services we use
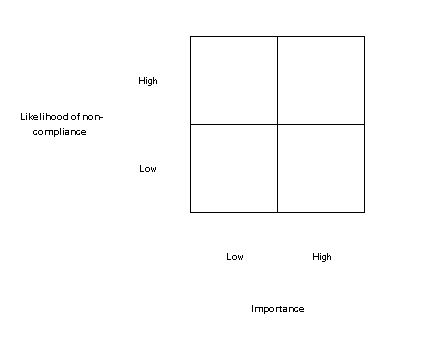
Naturally, the focus will be on the products and services where we have a high risk. This first step requires a lot of guesswork. Especially on the first attempt, it is very difficult to determine what can go wrong in another organization. And how this may affect our business. Nevertheless, I believe that a couple of iterations will result in a relatively accurate estimation of potential risks.
Supplier assessment
Collecting documentary evidence of compliance would be the start. So, for a start, request certifications related to SEE standards like
- Country-mandated standards
- Audits are done by relevant international or Government organizations
- International environment-related standards that provide certifications: ISO14001, GlobalGAP, organic manufacturer certifications
- Membership in organizations related to sustainable manufacturing and trade: Fair Trade, WFTO, Rainforest, etc
Secondly, request vendors to self-declare through a supplier declaration of conformity. While this is a good start, it needs to be well-created, so an audit can take place based on the document.
Supply Markets assessment
Here we are not trying to find out what is available with the vendors at the market. This is more about looking for technologies, solutions, and knowledge that will help us to reach our SEE goals. This is not something that can be solved with an RFI. Engage with vendors, visit trade shows and look at what research centers, universities, and institutions are doing.
Also, let us not forget governments here. Countries pledged not to allow new gasoline-powered vehicle registration after 2030. Moreover, they subsidize energy-efficient solutions. To take advantage of such options, we need to be aware of them.
Lifecycle cost and impact of main product categories
Most of us have calculated the total cost of ownership (TCO) during our careers. On this link, you can read a complete article on TCO. In short, TCO takes into consideration not only the purchase price of the asset but also all costs of running the machine and disposing of it at the end of its useful life.
Lifecycle costs add two more aspects that can be monetized:
- Company internal risks and benefits from the new asset. This is the influence of the new asset on the company besides the direct output of the asset
- Impact on society: changes in the number of employees, environmental impacts, and changes in the work environment.
Step 3: Develop a plan
Now we have our procedures in place. We have defined the risks related to SEE criteria. And we understand how SEE changes the way our company is doing business.
How does this change our day-to-day work in procurement?
Additional criteria in the RFQ process
Our requirements are now changing, as we want to have goods and services that are generating as little as possible harm to the environment. Hence we are establishing:
- Minimal requirements. Those are SEE-related specifications that are the bare minimum. If the company offers a product/service below those specifications, the offer will be rejected. Examples would be the usage of toxic material for packing, non-acceptance of the Supplier code of conduct, or similar.
- Optional requirements, where the supplier will get additional points in the RFQ process. As a result, we can award the contract to the supplier that has a slightly higher cost but has obtained extra points for his sustainable practices.
Audit plan
As always, the answer is: “it depends”.
Companies that employ large workforce:
Working hours and working conditions
Accommodations, if staff is living in company provided accommodation. Especially here it is important to look for records of building maintenance: fire fighting, pest control, and similar. The second point is to look into the food of the staff: do they have cooking facilities or the food is provided?
Companies that have processes including chemical
Certificates and inspection records about potential environmental issues? MSDS (material safety data sheets) for all products they produce. State of the storage.
Importers
Certificates of conformity with local laws. Also, it would be advisable to request the vendor to do a similar audit on their Tier 1 vendors, at least for modern slavery and environmental certificates
Changing the vendor evaluation points
Now we have one more area where we need to evaluate our vendor.
If we have done all stated earlier, we will have:
- The initial supplier assessment, with SEE-related documentation and certifications
- Audit report on the supplier, and hopefully a couple of his main Tier 1 suppliers
We will add this to our regular evaluation points dealing with the speed of delivery, quality, payment terms, etc.
This is a two-way discussion and process. In the start, especially if you are not working in (or importing from) developed countries, most of the vendors will fail the evaluation. The goal is not to keep changing them, but to upgrade the ones we would like to have as long-term partners.
Step 4: Measure
There are several indicators and goals that should be measured concerning ESG. For a start, I would recommend going ahead with simple ones:
- The ratio of compliant / non-compliant vendors
- Performed audits and audit grades
- Grievances recorded
These indicators focus only on the number of activities executed. While we are still not able to create an impact, at least we are raising awareness around the topic. Even if there are no repercussions due to a lower score, vendors will react and try to improve. In the second phase, after a couple of years, we will have enough data to see whether the overall performance of the supplier increases. Then we will be able to go into details and improvement plans and activities.
What I figured out during this process is that it is easy to overcomplicate things and try to cover everything. Not every company can tackle all aspects of Sustainability. And for sure we can not solve everything at once. So, the good old “one by one” rule applies here as well.
This is the first of the three blog posts on Sustainable procurement. In the second article, I will focus on organizational culture and mindset. The third post will focus on the practical application of sustainable procurement principles.
As an aspiring Supply chain manager,this is such an informative article. I have definitely learnt a great deal.
Thank you.
Thank you very much for your comment!
Pingback: Checklist for a good Procurement contract